Feeding
Automation Projects
Feeding
Cutting-edge solutions satisfying customer requests, providing flexible robotic automated lines for the most varied productions.
In particular, automations are provided with the use of anthropomorphic robots guided by neural cameras, developing the correct algorithms also in the organic sectors.
We also provide packaging and subdivision of materials by choosing and sorting them through digital vision
Installed systems:
Germany Cologne 2011, Italy Turin 2010.
Many other systems made in Italy from 2011 onwards, for Food Gadgets.
® Febo AP 2011
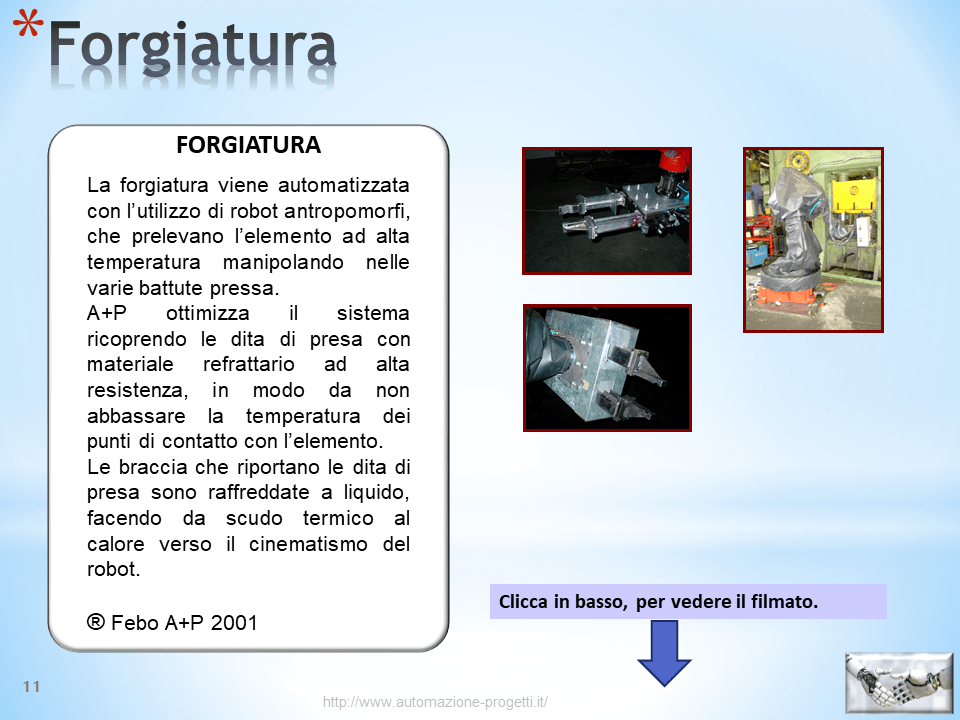
Robotized Forging
Automation Projects
FORGING
Forging is automated with the use of anthropomorphic robots, which pick up the element at a high temperature by manipulating it in the various press strokes. A P optimizes the system by covering the gripping fingers with highly resistant refractory material, so as not to lower the temperature of the points of contact with the element. The arms that bring the gripping fingers are liquid cooled, acting as a heat shield to the heat towards the robot's kinematics. Italy 2001 ® Febo AP 2001
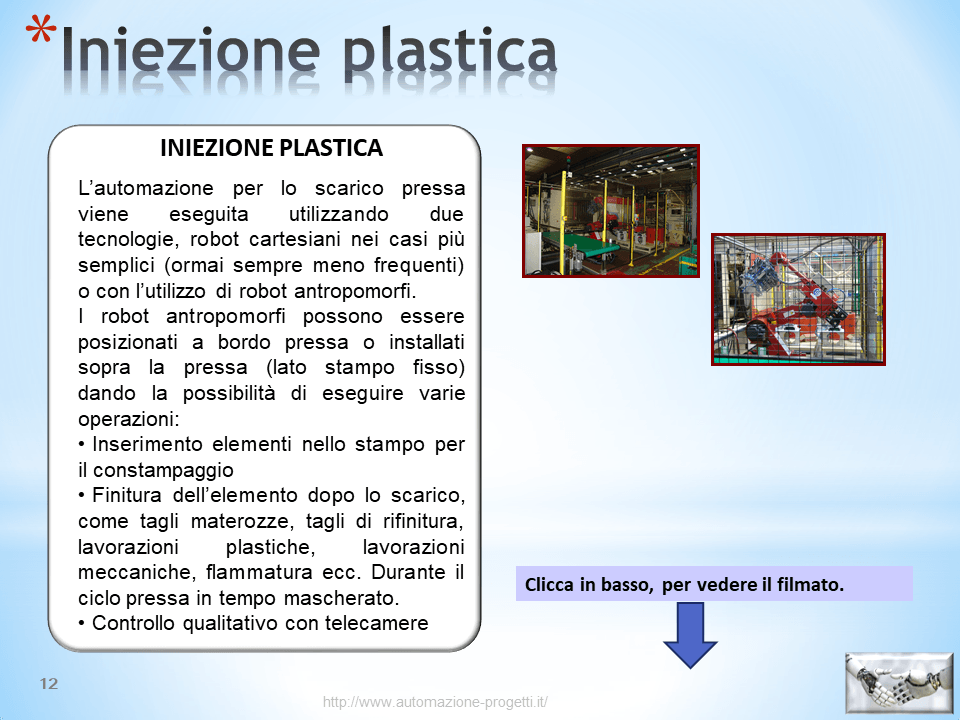
Plastic injection
Automation Projects
Automation for press unloading is performed using two technologies, Cartesian robots in the simplest cases (now increasingly less frequent) or with the use of anthropomorphic robots. The anthropomorphic robots can be positioned on the edge of the press or installed above the press (fixed mold side) giving the possibility to perform various operations: Inserting elements into the mold for co-molding Finishing the element after unloading, such as sprue cuts, finishing cuts, plastic processing, mechanical processing, flaming etc. During the press cycle in masked time. Quality control with cameras Installed systems: Italy, Spain, Belgium, Germany.
PLASTIC INJECTION 1
In this video, the robot synchronizes with the equipment, all managed by a single operator panel, which groups all the automation units, providing all production and anomaly data to the company server, obtaining total quality controlled at the 100%
PLASTIC INJECTION 2
In this video, a single robot performs multiple operations: 1. Sprue cutting 2. Materials objectification 3. Elements assembly 4. Subjective operations to the activities carried out 5. Testing at 100% Powerful, Precise, Delicate, Intelligent.
Robot with Multifunction Gripper
- The First Gripper contains embedded and protected the 2d camera and the laser sensor. With the Laser sensor the heights of the Layers are obtained, and the planes, even if inclined, the robot adapts to the plane detected by the Laser sensor. positions of the camshafts to be picked up.With the first gripper, the robot picks up the second gripper, passing it the electrical and pneumatic power supplies, for gripping the flats and intermediate layers.Automatic pallet changing system guarantees work continuity. Marpos control for the correction of the tolerances of the elements machined by the machine tool, through an algorithm with a derived base.
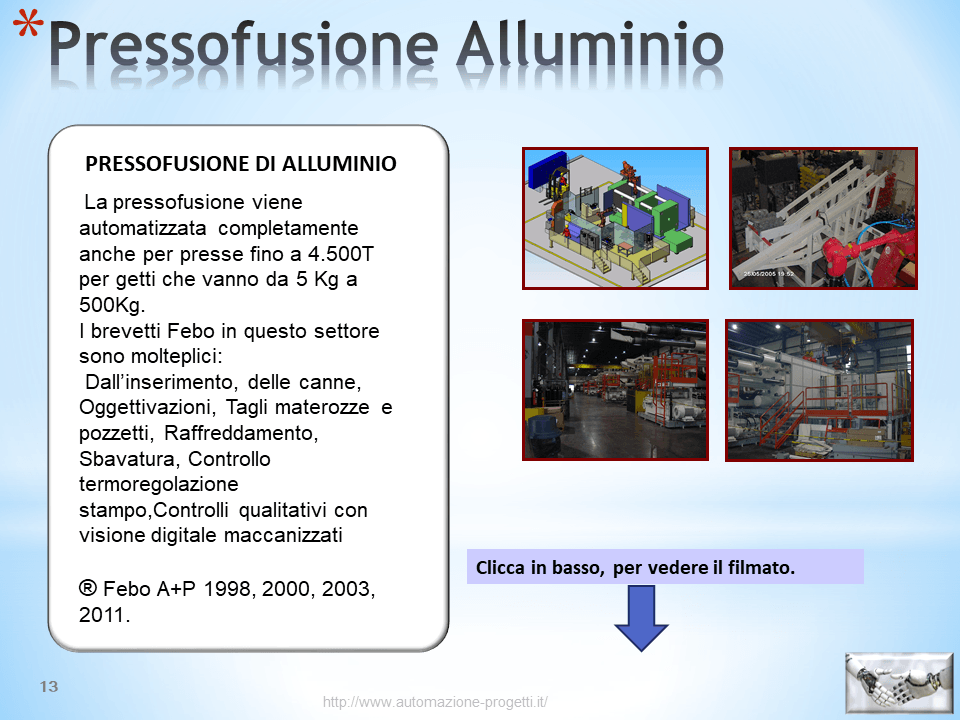
Aluminum die casting
Automation Projects
ALUMINUM DIE CASTING
Die casting is completely automated also for presses up to 4.500T for castings ranging from 5 Kg to 500Kg. The A P Febo patents in this sector are many: From the insertion of the rods, Objectifications, Sprue cuts and wells, Cooling, Deburring, Mold thermoregulation control. Machined quality controls with digital vision. Installed systems: Italy, Poland, Brazil, USA. ® Febo AP 1998, 2000, 2003, 2011.
ALABAMA
In this video you can see the first robotic automation in the die-casting sector in 1998, made in USA Alabama, in the Teksid plant which later became Nemak, and then continued in a long series of plants all over the world.
The customer and the operators were so enthusiastic and happy, also demonstrating it with a nice ballet that can be seen at the end of the video. 😊🕺 13 plants were subsequently built for the same customer in the same plant in Alabama.
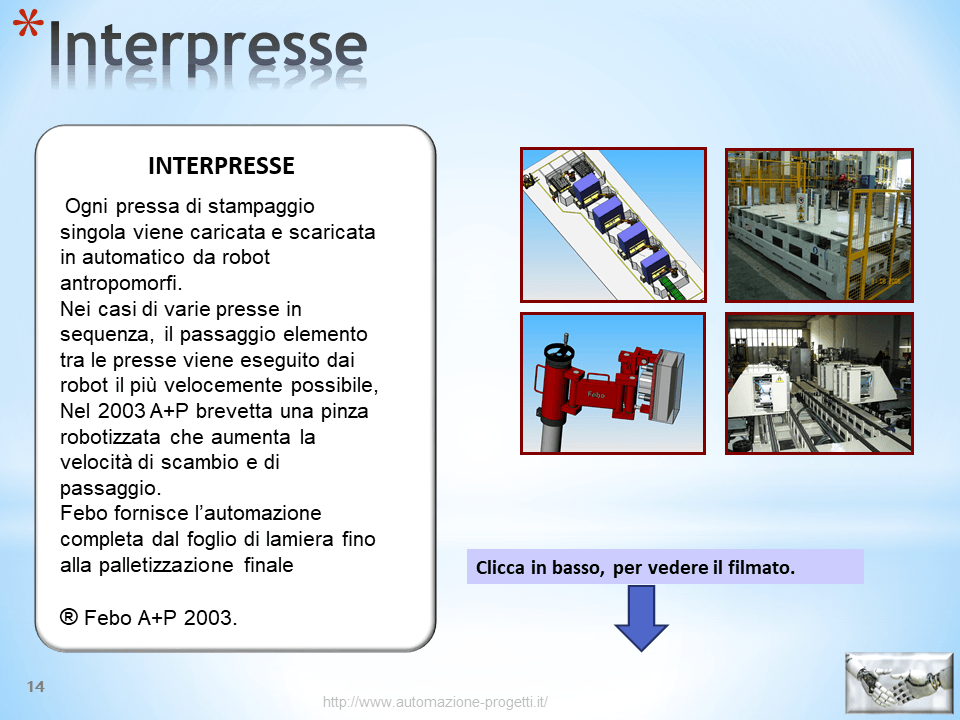
Interpresse
Automation Projects
INTERPRESSES
Each single molding press is loaded and unloaded automatically by anthropomorphic robots. In the cases of various presses in sequence, the element passage between the presses is performed by the robots as quickly as possible. In 2003 A P Febo patents a robotic gripper that increases the exchange and passage speed. A P provides complete automation from sheet metal to final palletization. Installed systems: Italy, Spain, Belgium, USA (Alabama, Tennessee, Detroit), Germany (with Muller Supplier Presse). ® Febo AP 2003.
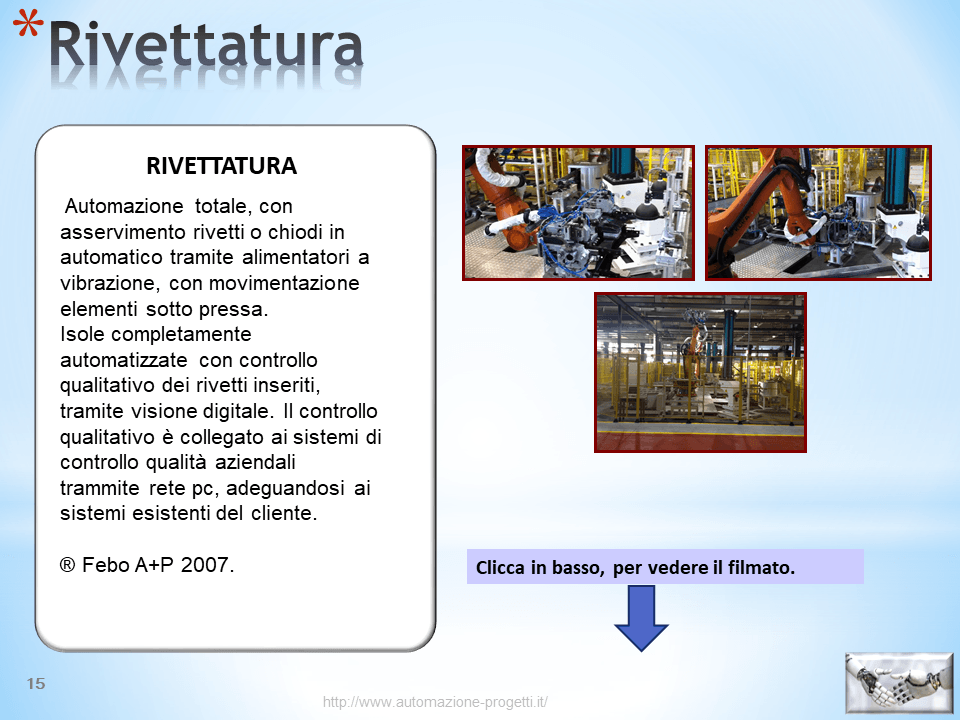
Riveting
Automation Projects
RIVETING Total automation,
with automatic interlocking of rivets or nails by vibrating feeders, with moving elements under the press. Fully automated islands with quality control of the rivets inserted, through digital vision. Quality control is connected to the company's quality control systems via a PC network, adapting to the customer's existing systems. Italy 2007 First plant for rear truck sleepers to use rivets instead of welds. ® Febo AP 2007.
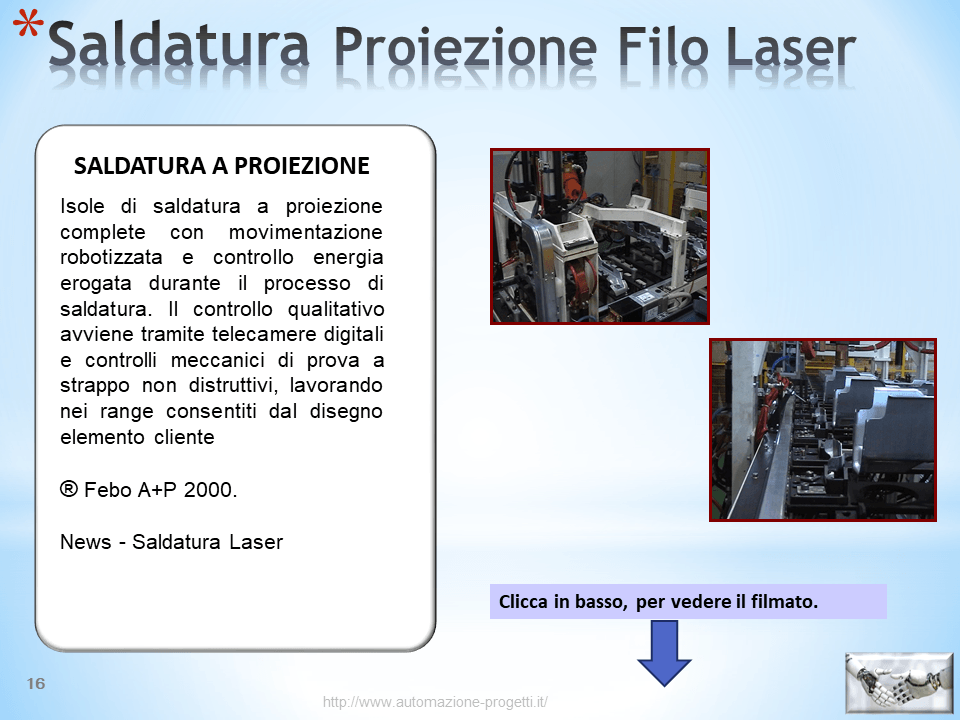
Laser Wire Projection Welding
Automation Projects
WELDING
Projection and wire welding islands complete with robotic handling and energy control delivered during the welding process. The quality control takes place through digital cameras and non-destructive tear-proof mechanical controls, working within the ranges allowed by the customer's design. Installed plants: Italy, Brazil, Poland, Spain, Belgium, Germany, Russia (Kaluga). Welding of Volvo aluminum tanks. ® Febo AP 2000. News - Laser welding
LASER WELDING News
Laser Welding Many advantages compared to the typical spot welding, with only one disadvantage, the price.
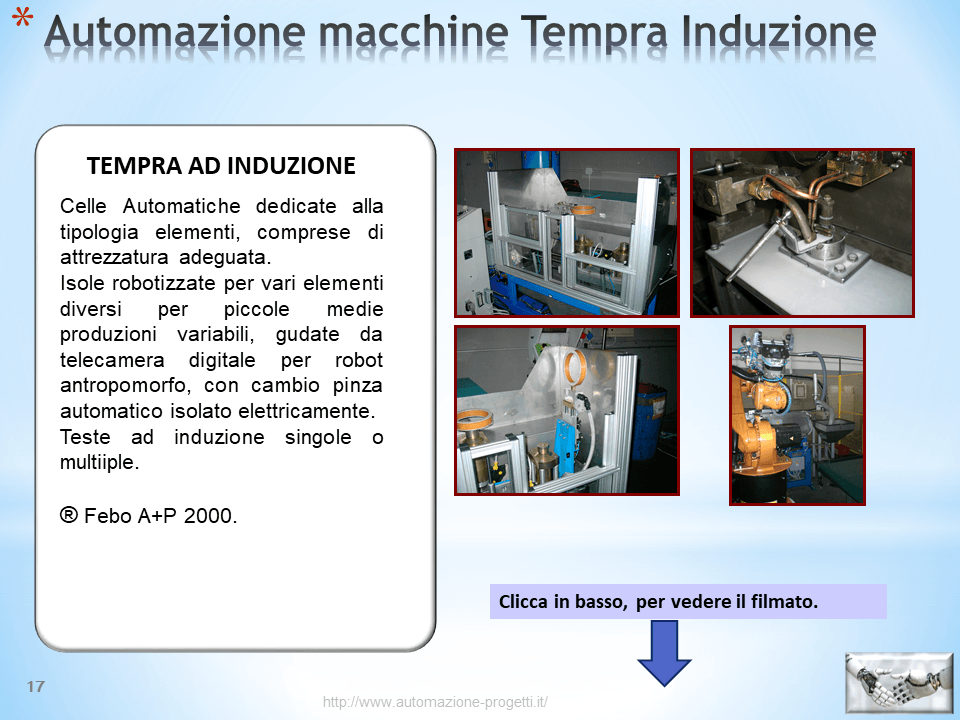
Induction hardening
Automation Projects
INDUCTION HARDENING
Automatic cells dedicated to the type of elements, including suitable equipment. Robotized islands for various different elements for small and medium variable productions, managed by a digital camera for anthropomorphic robots, with electrically insulated automatic gripper change. Single or multi-pole induction heads. Installed systems: Italy, Europe in general (Through customers Suppliers of heating heads) ® Febo AP 2000.
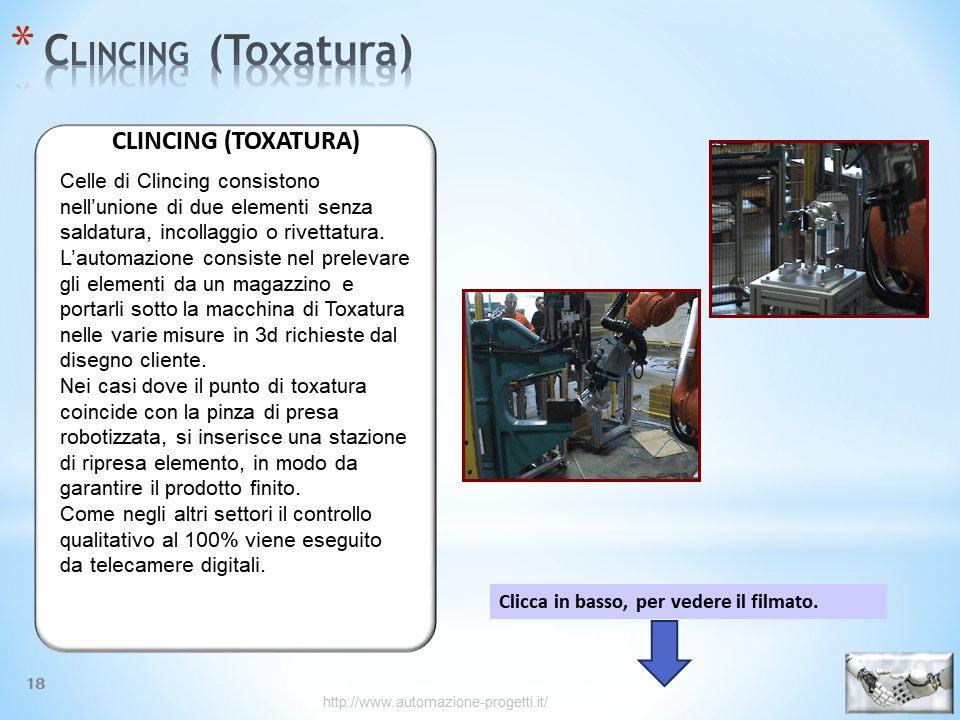
TOXATURA
Automation Projects
CLINCING (TOXATURA)
Clincing cells consist of joining two elements without welding, gluing or riveting. Automation consists in taking the elements from a warehouse and bringing them under the Toxatura machine in the various 3D sizes required by the customer's design. In cases where the toxing point coincides with the robotic gripper, an element recovery station is inserted, in order to guarantee the finished product. As in other sectors, 100% quality control is performed by digital cameras. Italy. 2000
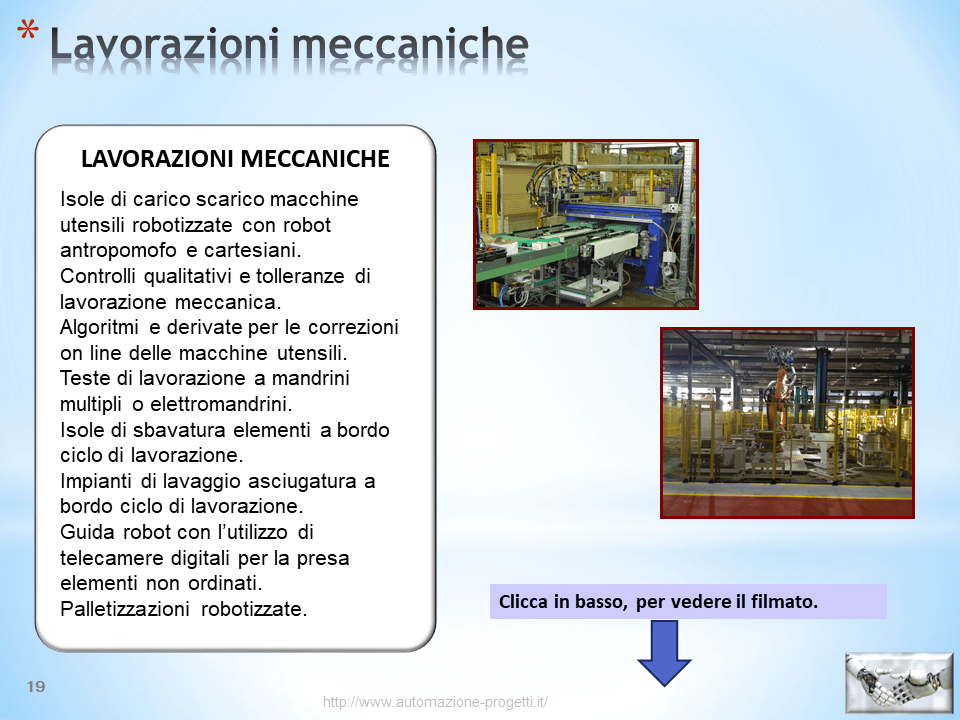
Mechanical processing
Automation Projects
MECHANICAL PROCESSING
Islands for loading and unloading robotic machine tools with anthropomophical and Cartesian robots. Quality controls and mechanical processing tolerances. Algorithms and derivatives for on-line corrections of machine tools. Machining heads with multiple spindles or electro spindles. Islands for deburring elements on the machining cycle. Washing drying systems on board the processing cycle. Guide robots with the use of digital cameras for taking unsorted items. Installed systems: Italy, Germany, Belgium, England, USA.
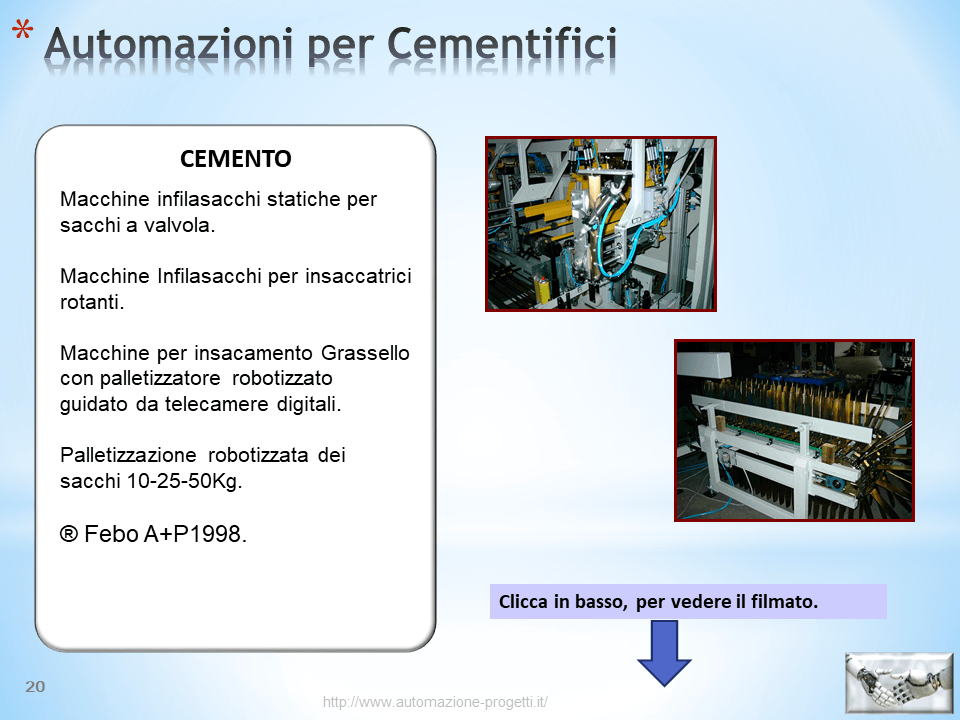
Cement
Automation Projects
CEMENT Automations for cement factories Static sack threading machines for valve sacks. Bag-threading machines for rotary bagging machines. Grassello bagging machines with robotic palletizer guided by digital cameras. Robotized palletization of 10-25-50Kg bags. Installed systems: Italy and the rest of the world. About 260 bag-threader machines have been sold in a few years. (Patent sold to the German bagging machine manufacturer "Our Customer" in 2001. Expiry of concessions 2018). ® Febo AP 1998.
Palletizers
Automation Projects
Palletizing
The Bottom Line A P, provides robotic palletizers for any type of material from packaging to bags for cement factories, flours, granules, fertilizers, etc. to any type of packaging in boxes. The long A P experiences cover palletizations for elements ranging from a few grams up to 1000 kg, using anthropomorphic robots. For heavier weights, tailor-made palletizers can be studied. Installed systems: Italy and the rest of Europe.
Special Palletization
Analyzing the customer's needs, we always propose simple and effective solutions.
We seek simplicity by facilitating the maintenance parts, thus obtaining very low MTBF - MTTR, limiting the time for interventions and maintenance.
Customer - Tetrapak and Italpak.
Flexible Palletization (Patents ® AP 1998 - 2013 - 2016)
From the 2000s onwards A P has developed palletizers with vision systems, in order to palletise different types of packages.
Create the platform with packages of very different weight and size, thanks to an algorithm developed to simulate the creation of the platforms by simulating size and weight, guiding the robots in building the platforms leaving the heaviest weights down.
Furthermore, in 2016 AP patents a robotic gripper that can pick up very heavy packs using a very low force between the gripping fingers, saving the integrity of the box also at a visual level.
One of the 3 patents in particular consists of:
in being able to reduce or increase the coefficient of friction between the gripping fingers automatically based on the size and weight to be handled.
So that the gripper can enter between the packs during picking by sliding smoothly, and then turn into high friction in picking conditions.
Customers still Top Secret Northern Italy, Germany.
® AP-Febo 1998 - 2013 - 2016.
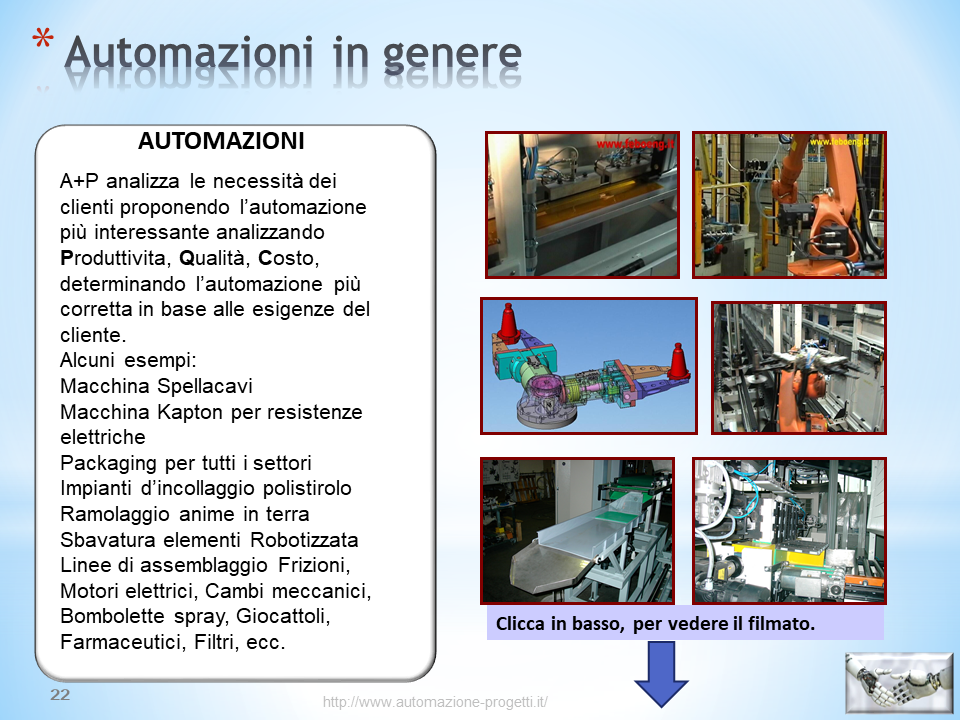
Automation in general
Automation Projects
AP AUTOMATIONS
Analyzes customer needs by proposing the most interesting automation by analyzing Productivity, Quality, Cost, determining the most correct automation based on customer needs. Some examples: Cable stripping machine Kapton machine for electric resistances Packaging for all sectors Polystyrene gluing systems Ground core deburring Robotized element deburring Assembly lines Clutches, Electric motors, Mechanical changes, Spray cans, Toys, Pharmaceuticals, Filters, etc. Installed systems: Italy, France (Valeo), Turkey, etc ...
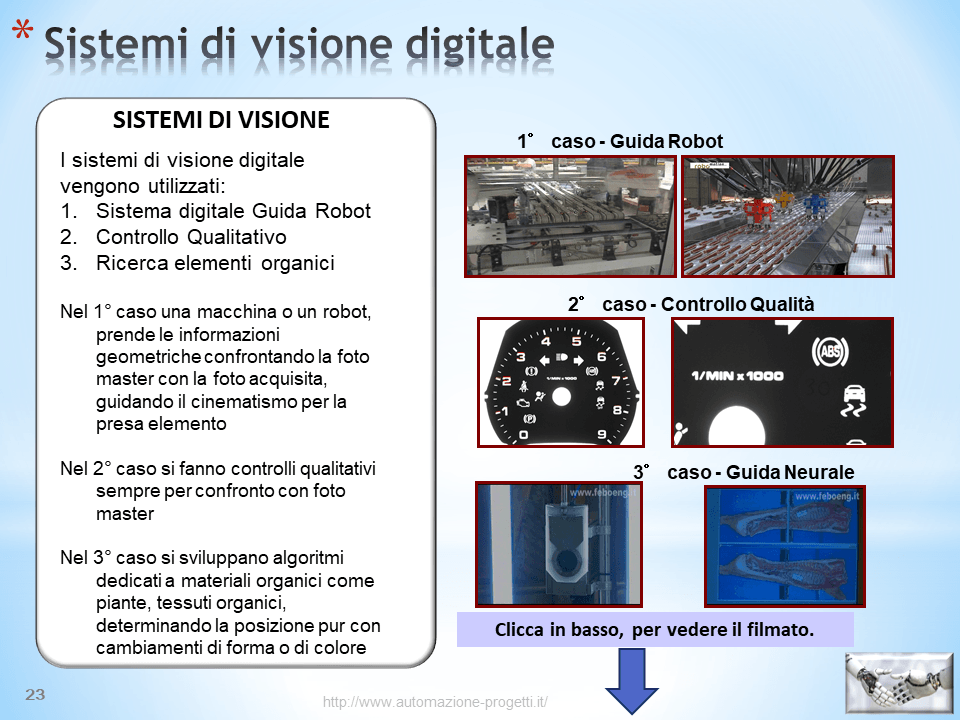
2D - 3D Vision Systems
Automation Projects
VISION SYSTEMS T he digital vision systems are used: 1-Digital Robot Guide System 2-Quality Control 3-Search for organic elements
In the 1st case a machine or a robot takes the geometric information by comparing the master photo with the acquired photo, guiding the kinematics for the element taking
In the 2nd case quality checks are always carried out by comparison with master photos
In the 3rd case, algorithms dedicated to organic materials such as plants, organic tissues are developed, determining the position even with changes in shape or color
AP builds sorting machines:
1 Vision systems for testing dedicated to customer needs, with stereoscopic 2D-3D vision.
2 In 2020 AP patents (together with the University technical staff) an innovative system for viewing the selected elements, with different lighting systems, in particular the same object can be illuminated with a backlit screen and with direct lighting at the same time.
Bin Picking
In this video, you can see objects of various kinds in different sectors, sorted with 2d and 3d vision technologies, which guide the anthropomorphic robots, to pick up elements directly from the bin or running on ribbons. With the same technology, digital references can be used to precisely match various types of elements including difficult elements such as transparent glass.
Customer Satisfaction and Operator Happiness are the basis of success. The solution to your Problem…. it is Our Work.